生産管理における在庫量と製造のリードタイムの関係とは
- 2019/7/1
- 生産管理
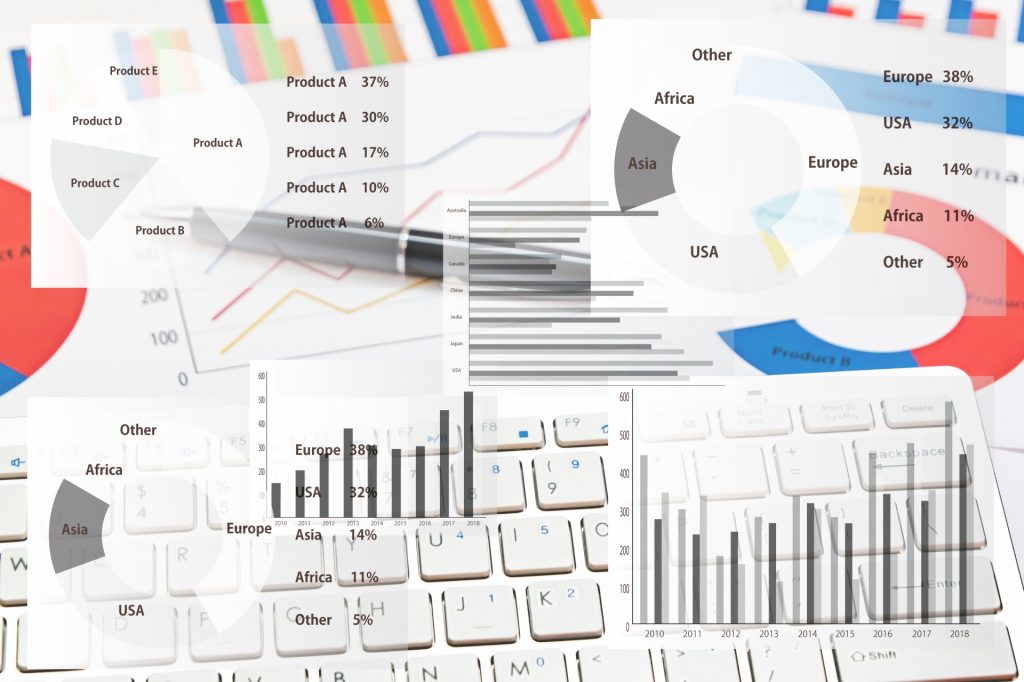
大量購入・大量生産方式でのスケールメリット
かつての高度成長期では大量購入・大量生産方式で大量の在庫を伴っていました。同時にそれなりのスケールメリットをもたらしサプライヤを含めて、在庫があれば後行程はいつでもその在庫を利用でき、販売にとっても便利で安心という考えが一般的だったのです。ところが今や低成長どころかゼロ成長であり、消費者の嗜好も多様化しています。いくら物を作っても思うように売れない状況です。
それにライバル企業も次々と新商品を誕生させています。いったん売れ残った商品は市場価格が著しく低下するのが実態です。まとめてたくさん作ることで、安く作ったつもりが売れ残って在庫になってしまえば資産でも何でもありません。在庫品を補完するための余計なコストがかかるだけです。いったん作りすぎの無駄を許してしまうと無駄が無駄を生むという悪循環に陥ってしまいます。ですからトヨタでは在庫は罪悪としていますし、必要数を厳しくとらえているのです。
必要なものを必要な時に作る時代
ここで必要数は市場の動向つまり売れ行きによって決まるだけに、工場側の段取り替えや手配の都合で勝手に決定できるものではありません。必要なものを必要な時に作るのが、これからの生産方式の基本的な考え方です。
機械をフルに動かして物を精いっぱい作るのが得だと考えるのではなく、売れるものだけ出来たらあとは機械を止めておきます。作っていくらではなく売っていくらのものづくり、余分なものは一切作らないことを基本とすべきです。ましてや今日のように市場のニーズが多様化して多品種少量生産が求められる時代では、量産によって原価を安くするモノ作りは通用しません。必要品目と限られた量をいかに安くタイムリーに作るかにかかっています。カスタマーイン、つまり売れに合わせたモノづくりへの転換なしには、企業の生き残りは難しいといえるでしょう。
リードタイムを考えること
生産管理で考える場合、在庫を持つリスクと、注文に合わせて生産するということではどちらがコストが高くかかってしまうのでしょうか。在庫があれば注文があればその在庫の中から商品を納入することができすぐに対応することができるのがメリットとなりますが、一体どんな商品の受注があるのかわからないので生産している製品すべてを在庫として持ち、保管することは大変なコストがかかってしまいます。もしも在庫として持っていた商品に一つも注文が入らなかったということになれば、その商品を生産したこと自体が損になり一円の利益もなくむしろ生産にかかった費用がすべて無駄になってしまうのです。
一方商品の注文を受けてから生産を行う場合、確実な注文なので確実に売ることができます。商品を作るためにはその商品が出来上がるまでのリードタイムというのがあり、注文をした人はそのリードタイムの時間分待っていれば確実に注文した商品が出来上がり、それを受け取ることが可能になるのです。受注があってから生産すれば無駄な在庫を持つこともなく確実にカスタマーの注文をさばくことができ、製造した側も確実に売れてよいことですし注文した側もリードタイム分待っていれば確実に製品を手にすることができるので、今後の予定も立てやすくなります。
在庫を持たないということは過剰納入、早期納入の防止にもなりますし現品管理の方式と事務処理を改善することができ、在庫不一致の早期発見とアクションも速やかに行うことができるのです。
在庫量と製造のリードタイムの関係
在庫量と製造のリードタイムの関係ですが売れる量が製品のリードタイムより早ければ在庫はなくなり、売れるのが遅ければ後工程で在庫となってしまいます。生産管理の仕方としては在庫が出ないようにリードタイムを調整するというのが、仕事となるのです。在庫を持たずに注文を受けてから生産開始し、出来たらすぐに出荷するこの方式が一番生産管理を行うことが簡単で棚卸などもスムーズに行えるのが特徴となっています。